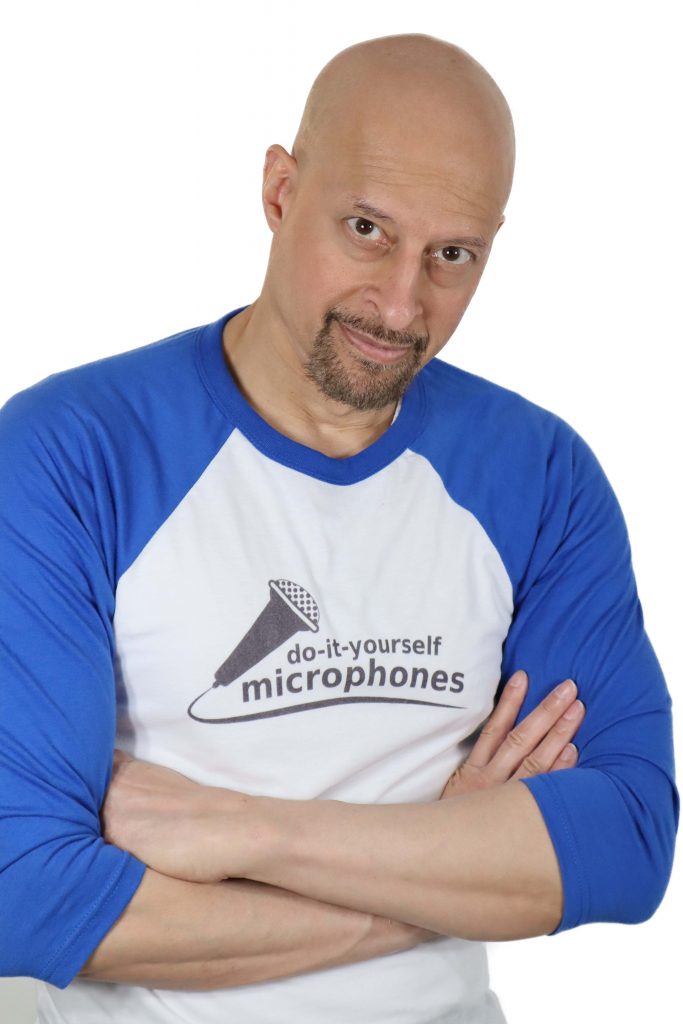
Hi, I’m the DIY microphone guy. I’m an electrical engineer and I like to build things.
I needed a microphone I couldn’t buy, so I built it—and I didn’t stop at just one microphone.
I decided to launch this site because it took me a long time to find the technical info I needed for my microphone projects, and I figured other people might have the same problem.
How did I get so interested in microphones?
As an electrical engineer, I’ve always had at least a passing interest in microphones, but that interest increased dramatically a few years ago when my wife decided to launch a YouTube channel. I was assigned the job of handling the behind-the-scenes technical stuff, while she created and presented the content.
As with many people first getting involved with YouTube, our audio set-up initially used an inexpensive field recorder and Electret Condenser Microphones (ECMs) that accept Plug-in-Power (PiP), all purchased from Amazon. So, my first DIY microphone projects focused on equalization to get the best sound quality from inexpensive PiP ECMs—first in post-production using equalizer effects in Premiere Pro, and later in real-time using Equalizer APO.
That initial set-up was more than good enough for our early YouTube activities. But while PiP ECMs are way cheaper than other types of microphone, they still seemed overpriced to me: more than $20 for a mediocre two-dollar ECM capsule, a few feet of shielded three-conductor cable, and a 3.5 mm plug. So my next DIY microphone projects were PiP microphones using high-performance ECM capsules.
Then COVID-19 struck, and we needed a way to record interviews without coming into physical contact with the interviewees. The video part was easy: we just used a slightly longer lens to put a bit more distance between the subject and the camera. But getting clean audio from more than a few feet away was challenging, and the shotgun microphones that were in our budget didn’t solve the problem. So I researched DIY alternatives to shotgun mics (including parabolic, horn, and array microphones) and built a few of each type. I also built a few actual shotgun mics, and pretty soon we had several DIY microphones that could meet our “socially-distanced” video production needs.
Then I wondered how far I could push the performance of inexpensive DIY long-range microphones. I have a friend who’s an avid bird-watcher and was thinking about buying an expensive commercial parabolic microphone, but wasn’t sure it would be worth the money. So I built some longer-range horn and parabolic microphones for him to evaluate, and he was happy enough with the results to forget about buying a commercial parabolic mic.
But when I started building long-range microphones, I needed a way to objectively measure their polar patterns and frequency response, which are major issues with any microphone that’s directional enough to capture sound at long ranges. That started me down the path of cost-effective equipment and techniques for microphone testing.
The next development was that we upgraded our audio recorders, and the new ones only accepted microphones with XLR connectors, and they only provided so-called phantom power for the microphone. This presented an immediate issue because all the microphones I had built or bought until then used Plug-In Power (PiP) and 3.5 mm TRS plugs. So I bought some ridiculously expensive XLR/phantom-power to 3.5 mm TRS/PiP adapters to get us going, while also launching an effort to design and test cost-effective DIY adapters and phantom-power circuits for ECMs and pre-amps.
And that brings us to today. We’re in the process of upgrading our audio set-up again, this time to improve the acoustics and reduce ambient noise in our studio. So my current focus is on DIY low-noise studio microphones, many of which use arrays of multiple microphone elements.
What’s next? DIY multichannel microphones, real-time hardware equalization using inexpensive Digital Signal Processing (DSP) boards, and DIY boom-arm setups are just a few projects currently in the pipeline.